Silomax Aluminum Silos
please contact us at
+90 216 709 26 00.
- OUR OTHER PRODUCTS
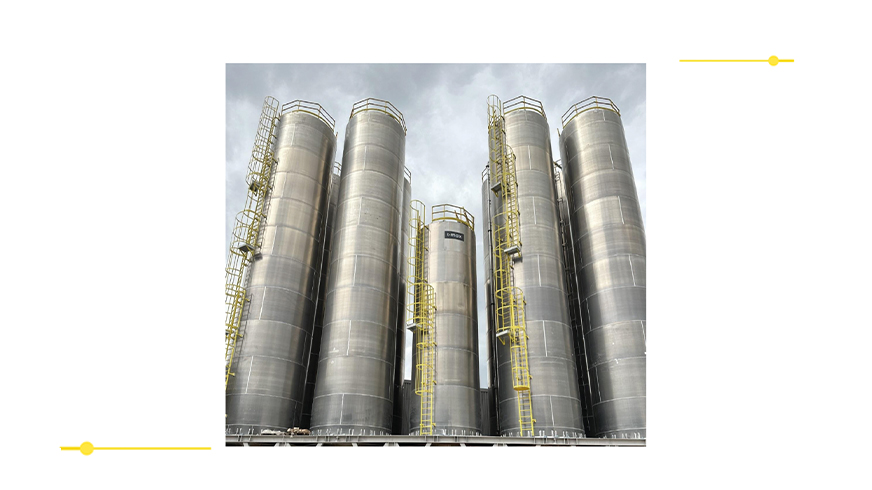
In today’s high-capacity plastic production facilities, silos are one of the most crucial components of automatic transfer systems, used for storage indoors or outdoors. This enables more efficient use of space in both indoor and outdoor areas while ensuring orderly storage processes.
Storage silos are typically made from aluminum or stainless steel (SST 304) materials, based on customer requirements. T-MAX offers both standard volume and ready-made silo models, as well as customized silo solutions tailored to customer needs and specifications.
Additionally, we provide solutions suitable for various materials such as crushing, PET flakes, dust-free fluidization, or any type of challenging flow, with a wide range of options available. We offer technical support to assist customers in selecting the right silo for their needs.
Silos help prevent raw materials from being affected by climate conditions, thereby aiding in the stable progress of the process. Commercially available plastics can be stored in silos without requiring any specific features, helping to preserve product quality and ensure timely delivery.
FEATURES
– Offers single or double-layered, long or short skirt designs.
– Available in special alloy aluminum or SST 304 material options.
– Utilizes modular panel silo design.
– Provides options for silo dimensions and volume tailored to the operating area.
– Delivered with many options included.
– Equipped with filling pipe.
– Provides connection points for level sensors.
– Includes manhole, air vent, and inspection ports on the silo roof.
– Includes climbing ladder, guardrails on the roof, and silo access pathways.
– Manufactured with a discharge angle of 600-900 depending on the material flow characteristics.
– Complies with seismic regulations, providing static and dynamic calculation reports.
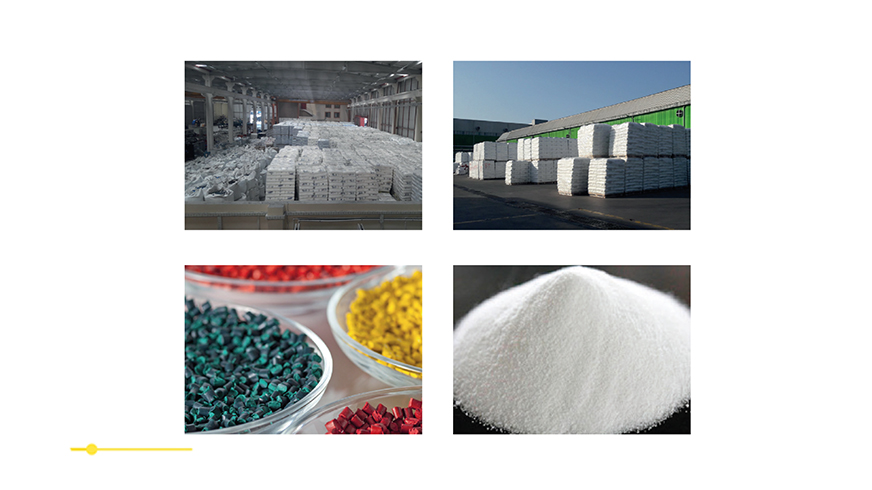
ADVANTAGES
– Offers long-lasting durability against corrosion.
– Can be easily and quickly installed.
– Allows direct filling from silo head, in-line container, or tanker, saving time and labor.
– Reduces costs of packaging such as bags, big bags, or octabins when bulk is received in containers.
– Eliminates demurrage costs with planned logistics activities.
– Prevents mixing with POKE-YOKE or coded silo filling connections.
– Enables real-time capacity monitoring inside the silo with min or max level and instant radar level control.
– Facilitates inter-departmental communication by transferring data to a server or local computer.
– Enables continuous monitoring and control of consumption with real-time reports.
– Provides engineering and technical consultancy services.
– COMPUTER-AIDED ANALYSIS AND DESIGN:
Computer-aided analysis is performed considering factors such as the area where the silo will be installed, seismic regulations, snow load, wind load, safety factor, and bulk density, depending on the customer’s request.
Based on this analysis, the required silo body thicknesses and foundation calculations are determined.
FEATURES
– Welding process is applied using special alloy or stainless steel material.
– Conical angle is adjusted according to the properties of the raw material.
– Real-time tracking of raw material stocks is possible.
– Provides a design with long-lasting durability against corrosion.
– Designed in compliance with food and job safety standards.
– Allows for easy and quick installation.
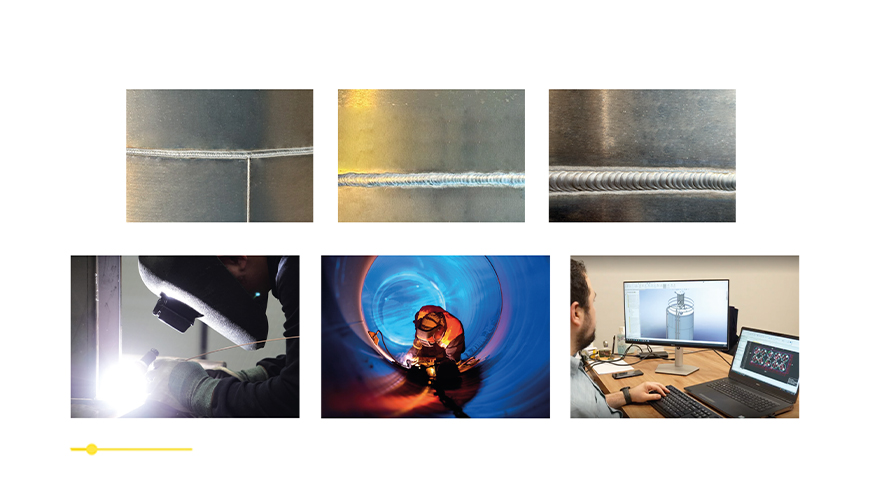
WELDING TECHNOLOGY:
Our silos, specially designed according to our customers’ requirements, are manufactured by our expert and internationally certified welders without compromising on technical and quality standards.
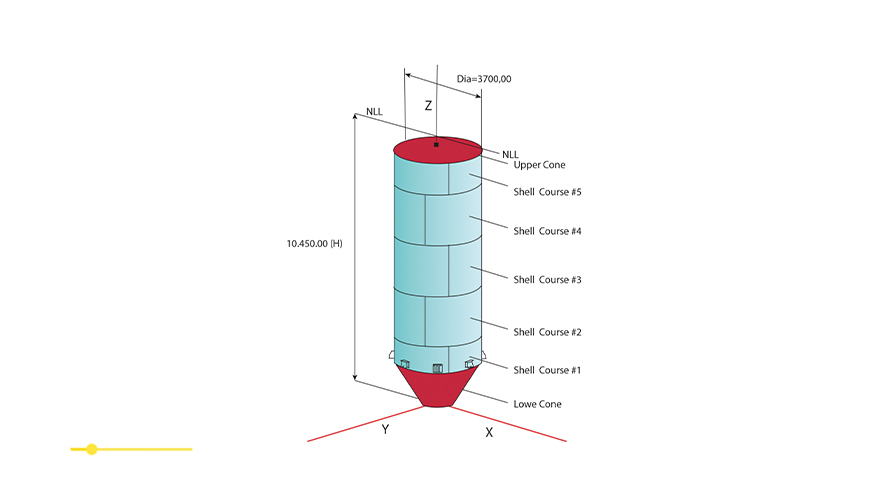
ADVANTAGES
– Eliminates storage costs in the production area.
– Prevents adverse effects of weather conditions on raw materials.
– Reduces the risk of foreign substances mixing with the raw material.
– Prevents unnecessary movement within the operation when used with a central loading system.
– Enables direct delivery of raw materials to machines.
To receive more detailed technical information about the product, please fill out the form below.
To access our product digital catalog, please fill out the form below.